The micro gravure coating technique is a coating method that is improved on the basis of ordinary reverse gravure coating technology. Its main technical features are kiss coating, reverse coating, and small diameter of the coating roller. The biggest difference between the micro gravure coating technology and the conventional gravure roll coating technique is that the ordinary gravure roll has a diameter of about 125 to 250 mm, and the micro gravure roll has a diameter of about 20 to 50 mm. The micro-gravure coating technology has a wet coating thickness of at least 0.8 to 2 μm and is more uniform. At present, the micro gravure coating technology is mainly used to prepare high-end film materials, such as high-end anti-counterfeit film, organic polymer conductive layer, lithium battery separator and other materials.
The intuitive result of the coating is the coating thickness, the factors affecting the coating thickness and the relationship between these influencing factors and the coating thickness are important for practical production. At present, the influencing factors of coating thickness are mainly studied at home and abroad through experiments and establishment of coating process models. In this paper, the factors affecting the coating thickness, the coating thickness measurement method, and the relationship between coating influence factors and coating thickness in the micro gravure coating technology are studied to provide a reference for the actual production of micro gravure coating.
Factors affecting coating thickness
Through the summary of the operational experience and theoretical research on the actual production of micro-gravure coating, the author summarizes the factors affecting the coating thickness into Figure 1.
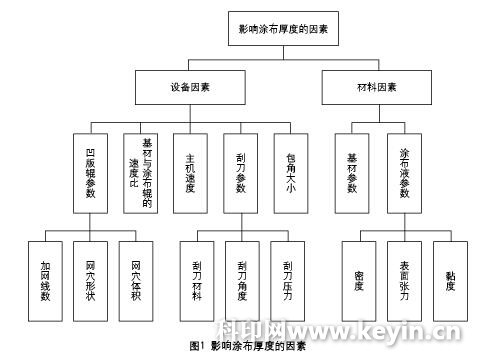
Equipment factor
Equipment factors primarily refer to factors that can be adjusted on the equipment. Among them, the micro gravure coating roller is a replaceable member, and the coating roller cannot undergo any change once the factors such as the number of screen lines and the shape of the cells are determined. General printing companies store multiple micro-gravure coating rolls according to production needs.
The speed ratio of the substrate to the coating roll (hereinafter referred to as "speed ratio") is another key factor determining the coating thickness. The speed ratio can be easily set via the device control panel.
In the scraper parameters, once the scraper type is determined, no further changes are made, and the scraper pressure and scraper angle can be adjusted by the cylinder change.
2. Material factors
When the coating liquid is determined, the coating thickness can be basically determined. If it is necessary to change, the ratio of the coating liquid can be changed by adding a solvent or the like, but the method takes a long time and is not in the actual production process. Too practical.
After the substrate is determined, the coating thickness can be changed by treating the surface or the like.
Method for measuring coating thickness
There are many methods for measuring the thickness of the coating. From the state of the coating, it can be classified into a wet film method and a dry film method.
The wet film method is generally on-machine inspection, that is, using a vertical electronic thickness gauge during the microgravure coating process to detect the coating thickness on-line. This method is quick to detect, can monitor the coating thickness in real time, and correct the problems in the coating process in time, but the vertical electronic thickness gauge is more expensive.
The dry film method is to measure the dry film thickness after drying of the coating layer, which is a relatively accurate measurement of the coating thickness, and the dry film method has many test methods and is economical, so it is widely used. The dry film method mainly includes direct measurement method and indirect measurement method. The direct measurement method is divided into a full-volume weighing method, a sampling weighing method, and a direct thickness measurement method. Among them, the whole weighing method is measured by an electronic weighing scale with an accuracy of 0.1kg; the sampling weighing method is measured by an electronic balance with an accuracy of 0.01mg; the direct thickness measurement method is to use a vertical electronic thickness gauge. Test with an accuracy of 1 μm. To ensure uniformity in the coating thickness test, multiple samples should be taken at different locations and averaged. The indirect measurement method mainly uses a scanning electron microscope with an accuracy of 50 to 200 nm, but the method has high measurement cost and long cycle, and is not commonly used in actual industrial production.
According to the test conditions and the advantages and disadvantages of each test method, the wet film method was used as the measurement method of the coating thickness.
Study on the relationship between influencing factors and coating thickness
1. Test equipment and materials
A lithium battery separator coater was used as a test device. The device uses a closed scraper type micro gravure coating unit, the substrate is suitable for PP film, PE lithium ion battery separator, the substrate roll diameter is 400mm, the width is 500mm; the slurry solute is nanometer powder, the solvent is water; the oven length It is 6 meters. The coating thickness was measured using a vertical electronic thickness gauge.
The test was conducted for the purpose of investigating the effect of the speed ratio, the host speed, the wrap angle and the blade pressure on the coating thickness.
Hospital Nursing Trolley,Nursing Cart,Convenient Nursing Trolley,Stainless Steel Nursing Trolley
NANJING TIANAO MEDICAL INSTRUMENTS MANUFACTURE CO.,LTD. , https://www.tianaomedical.com