As blow-fill-seal (BFS) technology matures, as single-dose packaging becomes more and more popular, and as manufacturers pay more and more attention to the aseptic process, the blow-fill-seal technology has become more The more popular it is. The most desirable feature of this technology is its prospects for advanced aseptic processing.
AstraZeneca Pharmaceuticals has first used BFS technology in Sweden, Australia and the United States, and is proud to have a strong network of experts who can exchange best practices across the globe for continuous improvement. Stability and work together. AstraZeneca began developing BFS technology in the 1980s when the company had just purchased a 10-chamber device from Rommelag. Prior to this, AstraZeneca had used a custom-made package for nasal drops. Blow molding machine.
With the commercialization of Pulmicort Respules asthma medicine, AstraZeneca's Westborough, USA, facility began large-scale deployment of BFS technology in the mid-1990s. The medicine was contained in a beautiful PP ampule and was inhaled by the patient through an atomizing device. At present, there are five Pulmicort asthma drug production lines in the factory, all using Rommelag 4010 equipment. The Westborough plant is currently regarded as AstraZeneca's superior BFS technology application center.
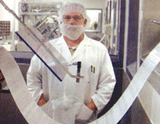
Next to Rommelag bag making machine
Install the production line according to the requirements of BFS
BFS technology not only brings AstraZeneca's advanced aseptic processing technology and class 100 cleanliness from the beginning of filling, but also reduces production costs and increases safety, said project engineer Mike Coyle. He witnessed the expansion of the plant and the experience of BFS. This growth also includes some design challenges (Coyle sees them as opportunities), especially to customize the filling equipment to meet the needs of products and processes. Among these challenges, the most important thing is to design a method to ensure that the budesonide particles (active ingredients of Pulmicort's asthma medicine) can be evenly distributed in each ampoule bottle. The solution is to design and implement a recirculation cycle between the machine's mixing chamber and the filling machine so that unused components can be returned to the mixing chamber and added back to the blend. This project required Rommelag to provide engineering support and build a prototype.
Another obstacle is to find a way to date each batch of asthma medicine bottles, batches and codes, and the risk of ink penetrating the PP bottle wall cannot occur. The initial production line was equipped with an inkjet printer and visual inspection system. "The FDA told us that 'you guys have to prove that it will not infiltrate, otherwise you will change this design'," Coyle said. They chose to change the design. Through technical assistance from AstraZeneca, Rommelag's engineers installed an embossing device on the production line to remove the surplus plastic from the filling mouth of each batch of bottles. Information such as batches, coding, etc. is directly imprinted on the bottle body. It took about a year and a half for the entire system to work properly, Coyle estimated. Other customization projects include separating the utility and aseptic processing parts of the equipment, generating stratified airflow in the sterile space, developing an aseptic suspension production method for equipment, and a sophisticated aseptic piping system.
Sophisticated equipment
Each BFS machine in the Westborough plant has 11 operating modes, including setup, cleaning, steaming, and production. Precise piping systems are controlled by a sophisticated and sophisticated valve system to ensure product purity. During commissioning, the valve status must be verified with the associated PLC and HMI settings for each operating mode.
The training the operator received for this equipment was very detailed, and Coyle said: “We have a group of technicians who have received special training for the mode switching operation of the processing equipment.†The training for them is in the supplier's factory. The middle school has already started, it is FAT test at that time, then continue in the field and off-field learning in the future.
The Westborough facility has automated its BFS operations as much as possible, although the operator is still critical to the entire process. The separate control system of the mixing zone and the Rommelag filler will show that a particular process has been prepared or completed. The operator is responsible for setting up the machine and transferring WFI or steam from the product tank to the filling mouth. In addition, depending on the actual situation (such as which tanks or transmission channels are being used within a certain period of time, or which machines are ready to start the production of a new batch of drugs), the operator will also need to participate in additional operations.
The key to ensuring advanced BFS process sterility standards is to reduce the number of operators entering the isolated processing space as much as possible. In certain situations where system closure must be broken (such as setup, machine maintenance or media filling), AstraZeneca's standard processes and workwear requirements can solve this problem. For some important issues (such as die chain rupture), the drug is aseptically recovered back into the tank under pressure. After the maintenance is over, fixed-point steam can restore the sterility of the entire system. Or, if the maintenance time needs to be extended further, the batch production may be transferred to another machine.
Integration and separation
Two of the five asthma medicine production lines were installed ten years ago in the then newly installed production workshop. The entire project was led by the Jacobs Engineering Group. The other three production lines were installed separately as production demand increased. One of them lifted the 4010 by a crane with a load of 300 tons, crossed a restaurant, and passed through a hole carved in the second floor of the building, Coyle recalled. The production line also shares preparation areas with the production line for injection drugs at the Westborough facility. This requires that the corresponding process, piping, and schedule be modified to support both the injection drug and the BFS area.
When the first two production lines were installed at the Westborough plant, they were fully integrated with the secondary packaging handling equipment. This is still the case today. After the product comes out of the filling machine, it will directly enter the conveyor belt leading to the packaging equipment.
When the third production line was installed, the factory decided to separate the filling and packaging operations. This is because the production speed of packaging equipment is much greater than that of BFS machines, so there is no point in making the efficiency of a packaging line limited by a filling machine.
Also, because BFS equipment is more reliable, it is not necessary for the front-end process to risk blocking due to subsequent packaging problems. "If BFS equipment is not integrated with the packaging line, downtime on the packaging line will not affect the continuous production of BFS equipment." Coyle said.
So for the 3rd, 4th, and 5th production lines, after the product comes out of the filling machine, it will go through the weighing and leak detection process, which is done by a Nikka Densok high-voltage pinhole inspection machine. The product is then placed in a tray and then transported by hand cart to the secondary packaging line.
Keep control
The operation on the mixing tank and the Rommelag filling machine is strictly controlled. Both devices are connected to a restricted local area network (LAN) to meet 12 CFR Part 11 requirements for backup and recovery.
When the third production line was being commissioned and certified in 2001, the FDA's guidance on 21 CFR Part 11 has changed, which has made it even more challenging to develop a computer-authentication (CV) module. Both the Rommelag HMI system and the preparation process control system require certification under the CV module.
However, the Westborough plant is still able to meet the delivery date for this production line. "We think that changes in requirements are not a problem, but rather an opportunity," Coyle said. "It gives us an opportunity to reconsider and improve the work we have done before."
The control system is supported by a SCADA system with alarm, reminder and information functions. The Westborough facility also maintains statistical process control functions for important parameters such as fill volume, vial thickness, and potion delivery.
&nbs
Who doesn't love a charcoal BBQ right? Charcoal BBQ makes the amazing smoky flavor of a steak and other foods. Families all have 3 or 4 Charcoal BBQs, all for different purposes. Whether it's a standard Kettle Grill, Portable Charcoal Grill , Tabletop Grill, Spit Roaster, Charcoal Smoker or a Kamado Grill. They all have a place in the backyard. We supply the latest design or custom-made Charcoal BBQ Grill, providing R&D Service exclusively for clients. Please feel free to contact with us for any features` grill you need, heavy-duty, easily cleaned.simply assembled and attractive look. Your Barbecues will be most salable!
Charcoal BBQ Grill
Charcoal BBQ Grill,Charcoal Grill,Outdoor Charcoal BBQ Grill,Spit Roaster
Dongguan Jiangxin Metal Products Co., Ltd , http://www.jiangxinbbq.com