Below, the author makes a simple analysis of the cause of the failure of the web offset press in the printing process and puts forward the corresponding processing methods, hoping to help the reader.
First, bad ink (blind version)
1, the ink part of the ink is not on the ink or a little fuzzy liquid acid to make the ink emulsification; ink roller pressure caused by ink roller deinking.
Processing method: replace the printing plate; adjust the pH value of the fountain solution; spray the reducing agent on the ink roller or stop cleaning the ink roller, and adjust the pressure between the ink roller and the plate cylinder.
2. The inked part is completely inky or repeated light marks appear on the same part of each page.
Cause: Blanket depression.
Remedy: Apply reductant or replace blanket on blanket.
Second, the entire surface of the printing plate stained with ink or ink stains occur when the reasons: the initial operation is stained with dry glue or dry plate when the machine is restarted; normal operation, a part of the water roller is not in contact with the plate, the brush roller Insufficient water pressure due to improper pressure on the fountain roller or abrasion of the brush roller.
Treatment method: Instantly increase the speed of the water supply motor to increase the amount of water so that the glue can be quickly removed. If it is not valid, it is necessary to check if the brush roller is worn. If the wear is serious, the brush roller needs to be replaced. If the wear is not serious, it is necessary to re-adjust the pressure of the brush roller, plate roller and water roller.
3. At the beginning of printing, the non-inking part was stained with a lot of paper powder. Cause: The printing began to dry. If the new ink reaches the front of the printing plate, the water roller will contact the plate for a long time. The plate will be contaminated; if it is not adjusted in advance, it will be in the ink. Printing is started when the roller is dry, which is particularly likely to cause this phenomenon.
Treatment method: stop immediately, wipe the layout. Then change the set time to start printing. Before restarting the machine, adjust the ink roller first. If we only increase the amount of water without shutting down the machine, not only can we not quickly remove the paper powder, but it will cause the imbalance of water and ink and the rejection rate to increase.
Fourth, bad words - text and outlets are damaged by ink Cause: excessive ink; ink viscosity is too high; ink roller pressure is too large; plate or blanket lining too thick; dampening fluid PH value is not appropriate; printing plate wear.
Processing method: reduce the speed of the ink supply motor or change the gap between the ink fountain and the ink fountain roller to reduce the ink volume; reduce the ink viscosity; re-adjust the pressure of the ink roller and the plate cylinder; reduce the thickness of the plate or blanket lining; change the fountain solution PH value; replace printing plate.
5. Particulate - Inked parts are thin and weak Cause: The speed of the water supply motor is too high; the ink is insufficient; the pressure of the plate cylinder and the blanket cylinder is insufficient; the blanket is cracked or stained; the printing plate is partially worn by the ink; the web paper powder excessive.
Treatment method: reduce the speed of the water supply motor; increase the gap between the ink fountain and the ink fountain roller to increase the ink volume; increase the thickness of the plate or rubber lining; wipe the blanket or replace the blanket; repair the plate or replace the plate; The tube paper is subjected to paper dust elimination treatment.
6. Paper fluffing and ring-shaped white spots - White spots on the printing surface, black spots on the non-inked areas. Causes: Contamination on blankets, ink rollers; Foreign matters in the ink; The surface of the blanket is sticky; Large causes paper fluffing; paper is too much on the web.
Treatment method: wipe the blanket and ink roller; replace the ink or add liquid to the ink, the original agent to reduce the viscosity of the ink; on the paper roll to eliminate paper processing.
Seventh, dirty version (dirty) - Non-inked part is stained with ink; ink viscosity is too high or too much ink to make non-ink-producing division pro-inking Cause: bad process of making plate; dirt on the water roller; ink Jumping or slippage caused by improper roll pressure; Blanking or damage of blankets; Improper pH of fountain solution or excessive water quality; Excessive humidity in the storage area of ​​printing plates.
Processing method: change the plate making process; clean the water roller; reset the pressure of the ink roller; tension the blanket or repair the blanket through the tensioner; adjust the pH of the fountain solution or add softener and ion agent after inspection. Change the storage conditions of printing plates.
VIII. Ghosting—Paper appears with horizontal light-colored stripes. Commonly, shadows are destroyed. Causes: Thickness of printing plates or rubber blankets; Excessive printing ink; Part of the ink on the printing plate is worn out; The pH of the fountain solution is poor.å«” å«” å«” å«” å«” å«” å«” 唤 唤 î¶è·Žç“’ î¶è·Žç“’ î¶è·Žç“’ î¶è·Žç“’ î¶è·Žç“’ æ¶£ æ¶£ æ¶£ æ¶£ æ¶£ æ¶£ æ¶£ 唤 唤 唤 唤 唤 唤 唤 唤 唤 唤 唤 唤 唤 唤 br br br br br br br br br br br br br br br br br br br br br br br br å¤„ç† br br br br br br br br ì´ Or change the gap between the ink fountain and the ink fountain roller to reduce the amount of ink; repair the printing plate or replace the printing plate; adjust the PH value of the fountain solution; increase the speed of the water supply motor, increase the amount of water, to prevent the ink on the plate from drying, and re-adjust the ink roller. Pressure; Check the parallelism of the ink roller rubber layer and replace the rubber roller if necessary.
Nine, ink roller ink failure - ink is not on the roller, the ink is not uniform part of the reason: ink roller pressure is not right; rubber roller wear or dents at both ends to make it bad contact; ink roller cracking; string ink roller, heavy roller coating Wear; the dampening solution is too acidic to emulsify the ink; the ink composition is not correct.
Treatment method: If the ink cannot be evenly inked, do not use strong roller pressure to operate. The pressure of the seal line of the roller should be uniform as a whole, and the pressure should be as small as possible within a range that does not affect the print quality. If the rubber roller is found to have worn or cracked phenomenon, it should be promptly replaced. The ink string roller and heavy roller coating should be promptly repaired if worn. Adjust the pH of the dampening solution or replace the ink.
Ten, floating dirty - the printing surface as a whole irregular light-colored dirt and whitening reasons: blanket cleaning agent into the fountain solution; too much water; ink viscosity is too high; ink is insufficient.
Treatment method: Change to a clean fountain solution; reduce the speed of the water supply motor to reduce the amount of water; reduce the viscosity of the ink with a reducing agent; increase the speed of the ink supply motor;
Eleven, take the paper slack - the paper between the printing press and folding machine slack reasons: roll paper power is too low; rubber blanket lining too thick; blanket paper powder accumulation; folding machine pulls the paper roll pressure Too low; the cutter roller (RTF roller) and the platen roller on the folding triangle are set badly.
Treatment method: increase the roll paper force by adjusting the spring or air pressure; change the blanket lining thickness; scrub the blanket; adjust the pressure of the paper-pulling roller and the pressure of the paper-cutting roller and the pressure roller until the paper is correctly fed.
12. Reasons for paper break: bad roll paper force or brake setting; excess amount of fountain solution; insufficient roll paper force; abnormality of the guide roller's parallelism.
Treatment method: Change the force of the web by adjusting the relevant elements, change the braking effect of the brake; reduce the amount of water; check the parallelism of the paper guide roller; replace the web.
XIII. Causes of paper creases: The blanket is dirty, damaged, slack, and the lining of the blanket cylinder is unsuitable; the amount of ink and dampening fluid is excessive; the tension of the web is too large; the parallelism of the paper guide roller is abnormal or the above There is ink and dirt; the folding machine is poorly adjusted; the web itself is defective.
Treatment method: Wipe method, tensioning blanket, change the thickness of its lining; reduce the amount of ink and water; reduce the roll paper force; wipe the paper guide roller, check the parallelism; readjust the folding machine; replace the roll paper.
Although with the development of computers, many problems can be solved by computers, but the analysis and processing of printing failures also require operators to continuously accumulate experience.
What are Baffled Bulk Bags?
Baffled Bulk Bags are truly versatile packing and storing solutions. These can be made using the U-Panel technique or the 4-Panel bag technique. It has a strong cubical shape which is composed of 4 separate vertical baffle panels. These are stitched inside the bags on the corners.
The baffle panels have efficient openings (ports) along the vertical length of the baffle panels. The openings (ports) can be made either round, oval, square, diamond and triangular in shape.
Baffled Bulk Bags offer highly convenient packing and storage solutions. These maintain the best square appearance and can be made in almost any size, on demand, apart from the numerous standard sizes that are available generally.
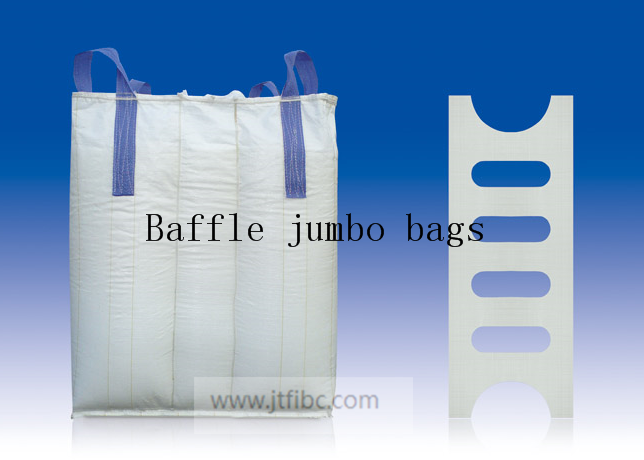
These are able to allow 25% more storage space as compared to standard FIBC. Cone bottom can be designed into the bag easily, according to requirement. The versatile bags offer higher efficiency in shipping and container storage.
Baffled Bulk Bags are most useful for storing low density products mainly. These are able to maintain the cube shape better and become ideal for storing powder, flake and other sifted products.
Baffle Bag,Mesh Bag Bulk,One Ton Bags,Fibc Bag
Shenzhen Riversky Packing Materials CO.,LTD , http://www.jtfibc.com